This article is published by Print Innovation Asia
With months of planning, MPS has held its first open house in Asia, at its new show room in Kuala Lumpur. Supported by many industry leading suppliers, the two day event has been hailed as a success by both visitors and suppliers who attended. We talked to Tim Klappe, Managing Director Asia Pacific at MPS.
What was the reason behind this open house?
TK. To show the print community in Asia Pacific what MPS stands for. The MPS Asia office was established back in 2018. We moved to our current office with showroom in 2019. However due to Covid, the decision to display a machine in the showroom was postponed.
MPS has a number of unique features in comparison with other suppliers in our market. For example our ability to show full insights in the performance and productivity of the press as the IOT (internet of things / sensor) -technology applied in the latest generation of MPS presses. The ability to run very thin foils (we ran 12 micron during the Open House) to card-board plus the ease of operation.
You have to see this yourself in order to believe it and see the difference, which is what we did at the open house.
Was the objective that you wanted to achieve reached?
TK. Absolutely, with over 130 people attending our Open House over two days. People were amazed when we sped up the press to 200 m/min while keeping an absolute stable register and sharp dots.
During the first day of the Open House we showed how easy it is to change from one job to another by using among others the job memory, the sliding out ink systems, automatic pressure control plus auto register. It's just so much easier these days
Over the 2 days how many people came to watch and learn.
TK. Over 130 people. During the first day we had the demonstration of the MPS EF Next Generation press and a number of presentations geared towards the production of pouches and shrink sleeves on narrow web presses. We had David Robbins from DIC and Steve Smith from Miraclon speaking about these topics. Further, Atze Bosma – CEO of MPS – spoke about the MPS vision and Frank ten Broeke of MPS spoke about our experiences in pouch and shrink sleeve production.
A narrow web press is more economical to use than gravure presses when you run jobs below 30,000 to 40,000 square meters. This is a very interesting space for printers as brand-owners demand more and more SKU’s and more frequent delivery times. The interest from flexible packaging printers was therefore high as well, nott only from label printers.
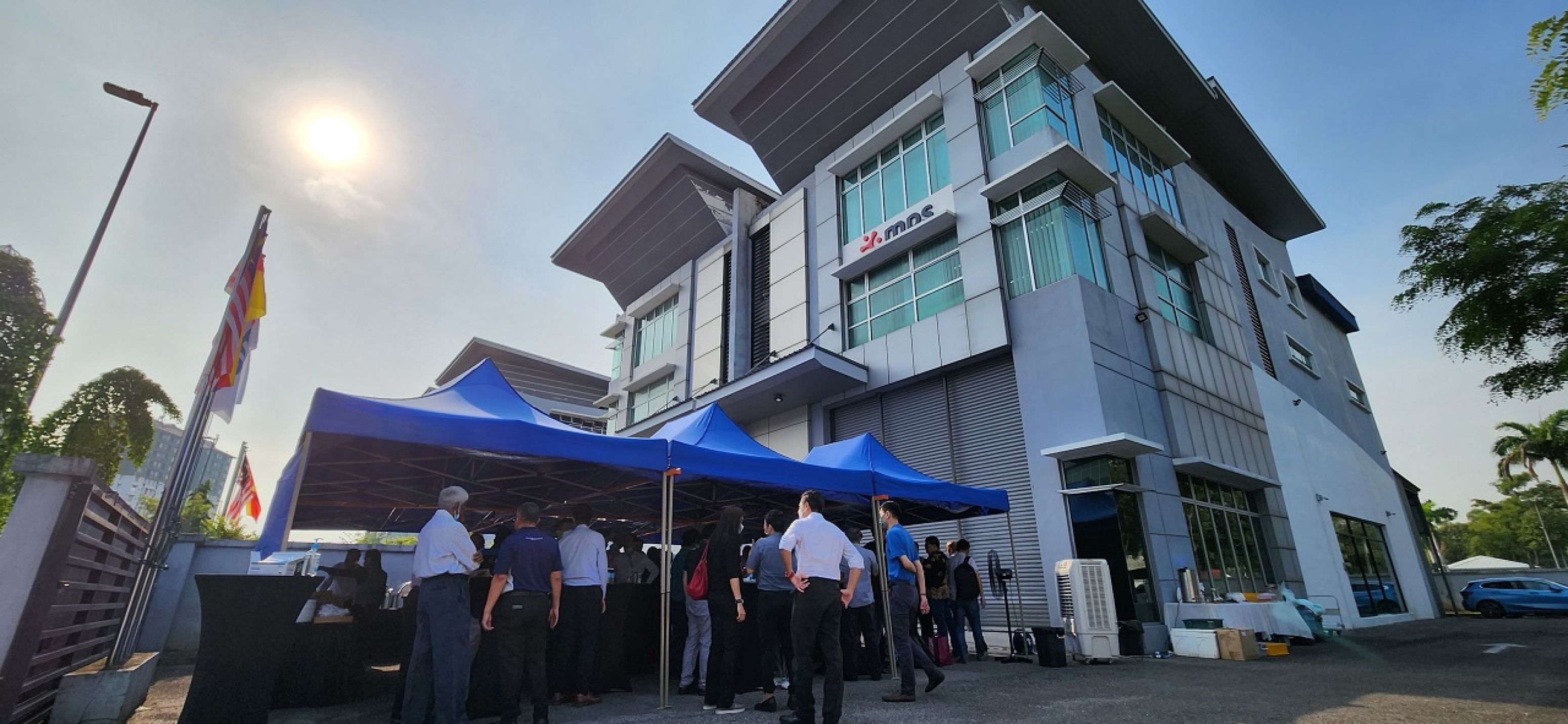
This is your new MPS demo centre of excellence in KL. What did you have going on for this event in terms of running machinery etc. What Jobs did you display live on the equipment.
TK. We had a EF-530 Next generation press with 8 EF flexo printing units with Hybrid UV and one EXL-p-530 unit. This means that the 8 EF units can run both LED and Mercury UV. The EXL-P unit comes in an antiexplosion cabinet and with an hot-airdryer. This makes it possible to print solvent inks, water-based inks and flexo UV inks in one unit.
We started with a shrink-sleeve on 40 micron nylon. We embellished the shrink sleeve with cast & cure. We can do this inline. A feature that is not possible with the gravure and CI presses.
After this first job, we changed to a 12 micron PET pouch top layer job in reversed print. These two jobs were all done in less than 20 minutes time. For companies that are into pouches and shrink sleeve production a very interesting and economical business opportunity.
What was the feedback you got from visitors? What was the one thing people keep looking for (ie machinery, Ideas on how to save costs, quality etc).
TK. A number of points seem to have caught our attention in particular. First of all, how very silent and smooth the MPS press is running. Even at high speeds from 150 m/min to even 200 m/min.
The fact that all data about the press operation is transparent. You know the set up times of the unwinder, rewinder, print sleeves, the set up time and printing time in total, the waste plus many details like tension settings and register setting. Productivity gaps can be seen with a glimpse of the eye. Ideal for productivity optimization.
The very easy way of setting up the machine. Thisis because of the operator panel on each printing station, the sliding out ink systems, the open concept of the machine and the rail for embellishment over the length of the press.
You had many companies join MPS for this event, what was the logic for this.
TK. To make a good pouch, shrink sleeve or label, you do not only need a good press. You need a good infra structure. From prepress, to press to finishing to inks, substrates, inspection systems, washing up solution, plates, anilox rollers, sticky tape, foils, etc. Everything should match together in order to get the highest productivity. For this reason, we invited partners in the industry.
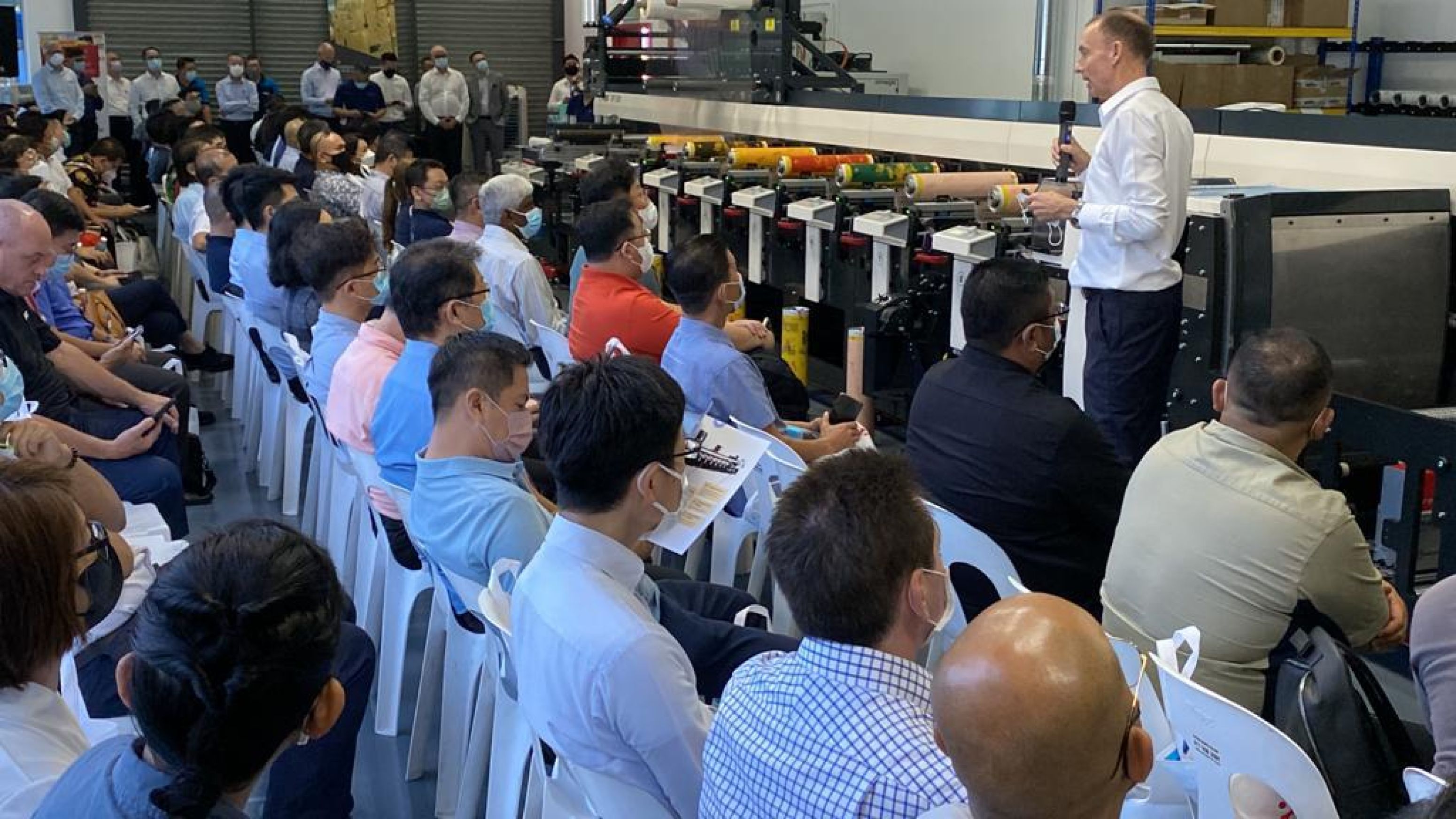
Tim Klappe, Managing Director Asia Pacific at MPS addressing the audience on day 1.
What was the feedback for the other solution partners at the event.
Here some reactions from our partners: It is valuable to learn how connectivity and its implementation can be made a breeze, to help business owners understand their processes and make more informed decisions. We are honoured to be part of this.
Peter Goh Yong Long | Sales Manager Singapore & Malaysia | ESKO
From day one, our partnership and vision alignment with MPS has resulted in a strong collaboration and joint commitment to its development and market success in Southeast Asia. The outstanding open house event delivered by the MPS team showcased the value of their expertise as a visionary press manufacturer. The quick changeover of the MPS press resulted in coming up to speed at 200m/min with superb quality while rapidly utilizing DIC LED inks, demonstrating the strength of two market leaders.
David Robins | Regional Sales & Marketing Manager Flexo Ink Business and Regional Accounts Management, AP Region | DIC
I am completely convinced of the MPSConnect programme. It is a very concrete step towards realizing sustainable development goals, and will certainly help manufacturers and converters achieve ‘responsible consumption and production goals’. It is a simple, clear, and easy to apply PDCA process.
Hoang Ha | C.illies Vietnam
As a key supplier to MPS, BST was very pleased to be invited to participate in what turned out to be a hugely successful open house and seminar. Traditionally, it has been very difficult to penetrate the wide web gravure and flexo film converting market with an alternative narrow web solution; the demonstrated EF-530 press clearly shows that this divide can be crossed.
The press was equipped with BST web guiding, web viewing, and web monitoring systems and as a regionally based subsidiary, BST South East Asia is committed to supporting MPS in the region both from a commercial and technical standpoint.
Albert Tan | Regional Sales – Malaysia | BST
Böttcher is proud to be a supply chain partner of MPS Systems, known as providing one of the highest flexo printing press in productivity. The two-day event organized by MPS Systems Asia successfully demonstrated and proved the MPS EF series to participating printers. It was an amazing event, bringing printers together from around the Asia-Pacific region. Great effort and commendable work from the entire MPS Systems Asia team!
Kenny Loo | Managing Director | Böttcher Malaysia
We would like to thank MPS Systems Asia for inviting Miraclon to collaborate and present at their open house, one of the first in-person joint partner events we have had in the Asia-Pacific region since travel has normalized. It was a very successful event and provided us with an opportunity to exchange information with MPS as well as other industry leaders. By working together with innovative partners like MPS, we can further our vision of ‘Transforming Flexo Together’ and help packaging printers maximise performance and exceed quality expectations of brand owners.
Joerg Kullwitz | Regional Commercial Director, Asia Pacific at Miraclon
This partnership event with MPS brought together the latest flexo technologies and designs to make the printer’s life easier. It is all about combined solutions to allow printers to complete complicated jobs with high print quality, cost-effectively, and with process efficiency. For plate mounting tape choices, tesa is happy to land on a solution that fits the application.
Stephanie Lee | Regional Key Account Manager, AP | tesa tape Asia Pacific Pte Ltd
The overwhelming attendance at the MPS Systems Asia open house event is evidence of great interest by the industry, especially in the flexible film packaging segment where there’s growing demand for shorter print runs.
The live print demonstration clearly showcased the capability and efficiency of the MPS press which includes quick machine setup time, fast print speed with consistency, swift registration, less waste, and more. It was particularly interesting to see the subject of machine uptime/ utilisation mentioned by one of the guest speakers arouse the attendees’ interest.
Sam Seow | Sales Director of Asia Pacific | APEX International
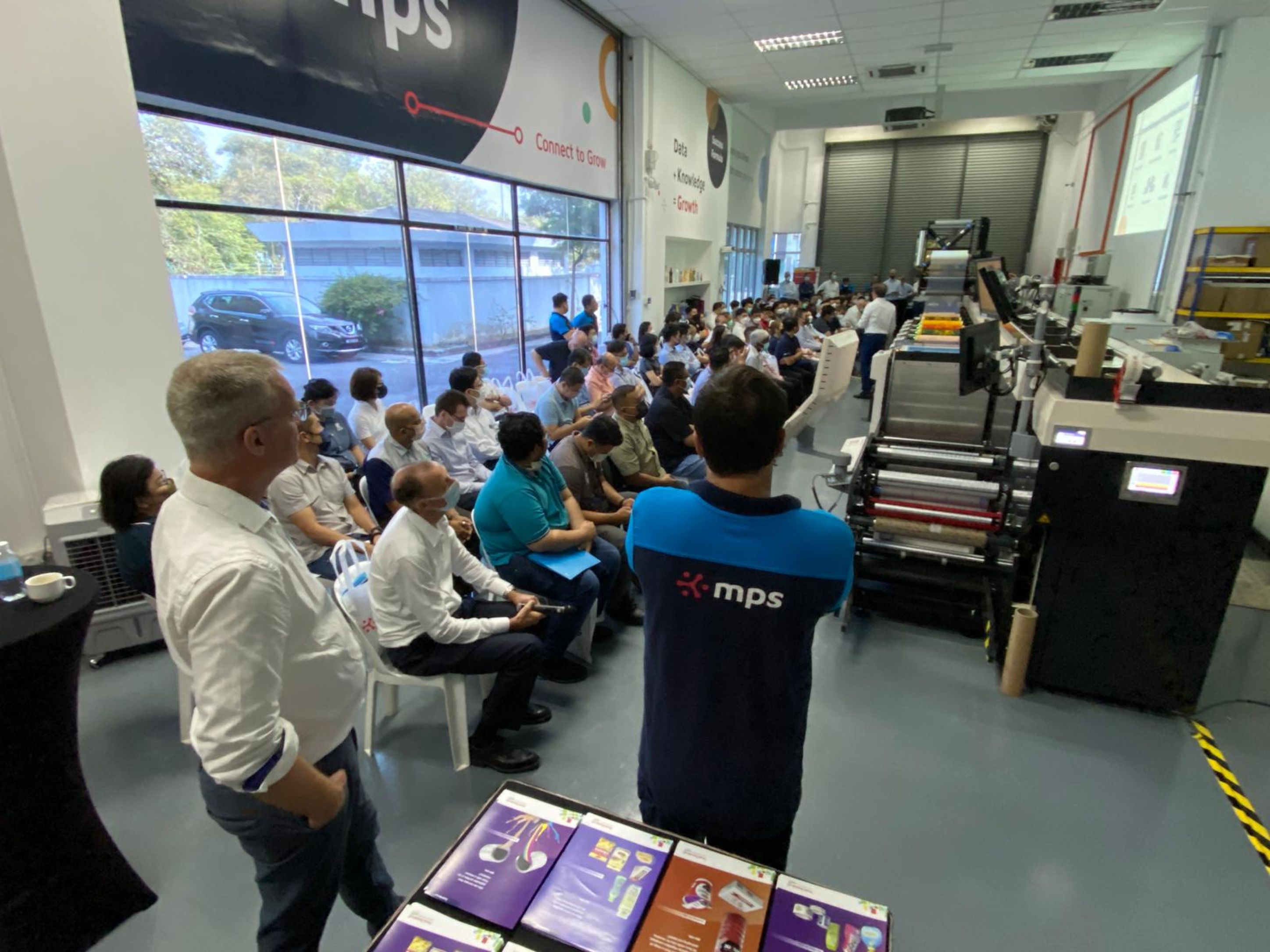
Will this become a regular fixture on the MPS Asia calendar for the future.
TK. We truly hope so and want it to be. The machine that we currently have in our showroom will stay here till the end of this year. We are working already on our next showroom machine.
What is on the MPS radar looking into the near future in Asia Pacific.
TK. With more installations in the Asia Pacific region, we will continue to build up our team . We are planning to roll out a set of training. The most interesting program that we have rolled out already is a program to guide our customers in achieving higher productivity. In this program we are the facilitator who comes with a set of tools and expertise from several disciplines.
For example, benchmarking and full insights in the productivity of a press shows immediately where potential areas of improvement are. Exchanging information on best practices enables the first quick wins. Further, we use 5S concepts, deep dives from our data analysts and experience from our team to fine tune productivity further. This program takes one year.
The gains achieved by our customers via this program is enormous. So, although MPS manufactures machines, our concept goes far beyond the machines. Our vision is to enable top productivity by our customers. Not just by having a top printing press. But, being organized in the most productive way.